Dispersed printed fabric is a versatile and flexible printing technique that enables designers to create intricate patterns, delicate motifs, and even photorealistic imagery with exceptional clarity. Compared to other print methods, dispersed dye printing offers the advantage of colorfastness, making it ideal for use in garments and textile products that will be subjected to frequent washing and exposure to sunlight. It also offers a high level of customization, as designers can choose from a wide range of colors, allowing them to match the fabric’s aesthetic and functional requirements.
The dispersed dyes used in this type of printing are chemically bonded to the cotton fibers using an alkaline solution, which makes the printed design permanent. The dyes are also able to penetrate the fibers, resulting in vibrant and long-lasting colors. In addition, the dyes are able to resist fading and color-to-washfastness is good. Disperse dye printing is typically suited for fabrics such as cotton and polyester that require a durable finish.
In contrast, pigment printing is a process that requires the use of adhesive and cross-linking agents to permanently bond the pigments to the surface of the cloth. However, unlike the disperse dye method, pigment printing is suitable for a variety of fabrics including silk and wool, as well as natural fibers such as linen and cotton.
To improve the migration-diffusion of disperse dyes ink, it is important to select an ink carrier with a low solubility parameter, a high molecular weight, and excellent adhesion properties. This can improve the ability of the ink to wick through the cotton fibers, thus facilitating the penetration of the dyes. The solubility parameter of the ink additive should also be closely matched to that of the dyes, as this will help to reduce the opacity of the ink and increase its transparency.
After printing, the fabric is steamed to set the dyes and can be fixed by three different methods: (1) Steaming at disconnected pressure: Printed fabrics are steamed for 30 minutes at 128oC (30 psi). This method provides full color yield and bright prints, but is more labor-intensive than the other fixation methods.
(2) Alkali padding and indoor-temperature stacking: Printed fabrics are alkali padded with a mixture of calcium carbonate, sodium hydroxide, and water. The printed fabrics are then stacked and exposed to heat at a temperature of 210oC for 30 seconds. This method produces a good dye utilization rate, and the dyes are deeply printed into the cotton fibers.
(3) Thermofixation: Printed fabrics are thermofixed in an autoclave at 210oC for 30 seconds. This system is more efficient than the other two methods and requires a lower temperature.
All the printed samples exhibit very good wash, perspiration, and rubbing fastness, which means that they are able to withstand a large number of washes without losing their vibrant colors or quality. The PVA and PEG ink-added printed fabrics exhibit better print clarity than the control sample, due to their superior viscosity. The PVA ink also exhibits good adhesion to the fibers, whereas the PEG ink shows a tendency to migrate from the surface of the fabric.
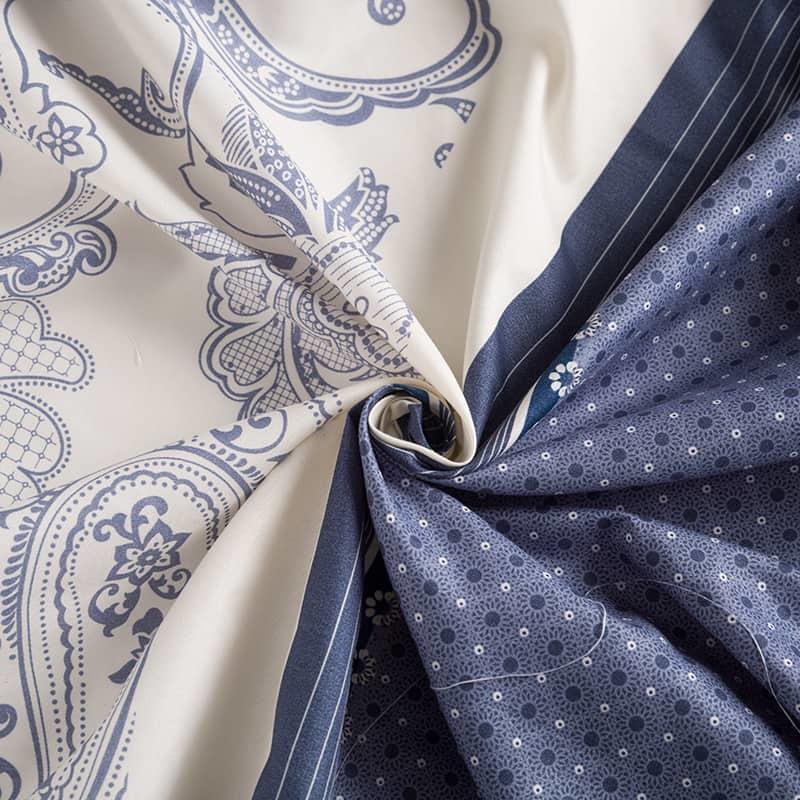